SINORA transport cases are manufactured from the resistant plastic polypropylene (PP) using the injection moulding process. The precision of the injection-moulded parts produced makes this process particularly popular and offers clear advantages over rotational moulding or deep-drawing processes.
The production process summarised in five steps:
- Plasticising the plastic granulate using heat
- Injection into the mould under high pressure
- Pressing during the cooling process
- Cooling of the injection mould
- Demoulding of the finished plastic part
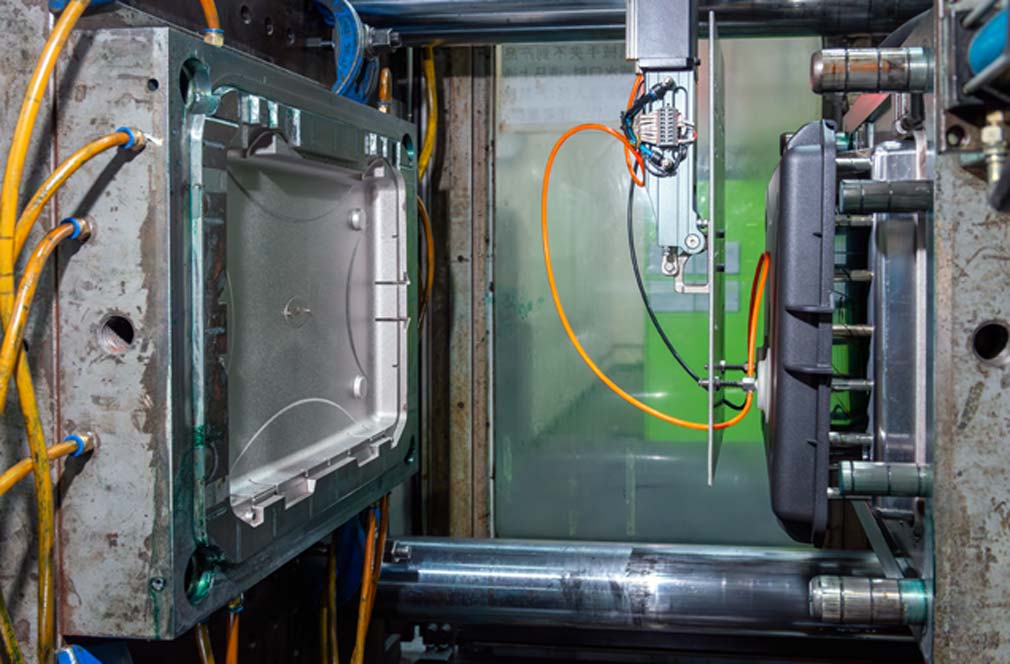
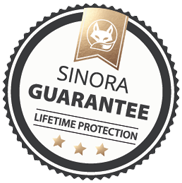
Integrated toolmaking
Customized precision through in-house toolmaking
We define innovation, quality and flexibility through our in-house toolmaking department and state-of-the-art machinery for injection moulding machines. This integration enables SINORA to respond directly to individual customer requirements and create customised, high-precision injection moulding cases.
Our machine park comprises 12 injection moulding machines with a clamping force of 80 to 2100 tonnes. This optimal equipment enables us to produce small to very large injection moulded cases that meet the requirements of a wide range of industries.
SINORA is characterised by its ability to react quickly, which is guaranteed by its integrated toolmaking department. Our efficiency and cost-effectiveness are reflected in an impressive production capacity of over 20,000 cases per month.
Describe your requirements to us – we will be happy to advise you!
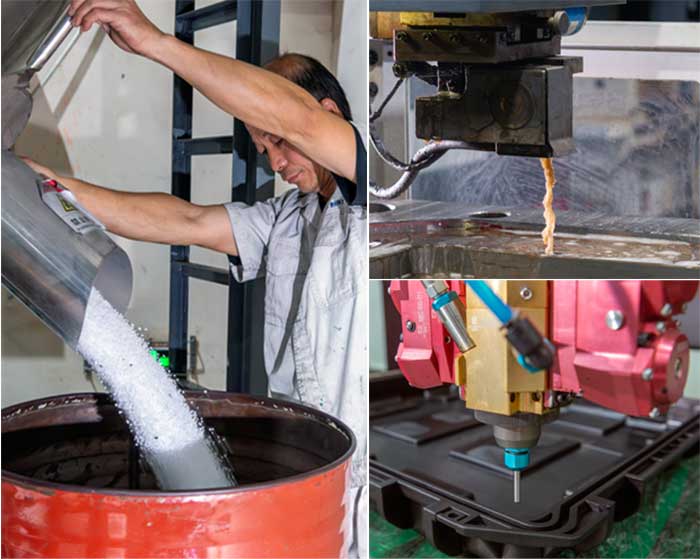
Order protective and transport cases online
Directly to the online shop